Silicon rubber keys of Screen Printing Technology
This article describes the silicone rubber screen printing process, analyzes its ordinary screen printing technology differences to explain its technical features, and summarized in the technical control of their own views. Keywords: silicone rubber screen printing silk screen printing quality silicon rubber keypads silicone rubber keypad features
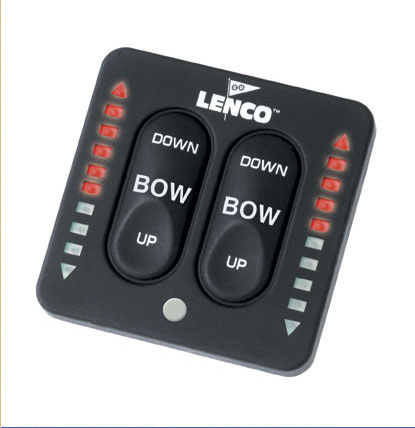 As the communications, the rapid development of electronics industry, rubber production has also become a key a mature technology. The key products from silicone rubber molding at high temperature to form the required button key surface that, through spraying, screen printing, the processes of the formation of red peel. I am here to make this preliminary study screen printing process. First, the characteristics of silicon rubber keypads As the key material of silicone rubber, hardness generally 45 ° about printing surface with a single key convex, concave surface and the plane alone, all the field lines of print. In addition to required position accurately printing, graphic clarity, but also required for the printing ink silicone rubber, ink reaches a certain thickness, strong adhesion and abrasion resistance, high temperature baking does not change the color. So it made screen printing process more specific technical requirements. 2, Screen Printing Method of screen printing plate more, mainly photographic plate method, that is, directly to the photoresist on the Internet, dry after a certain thickness of the photosensitive film as vector graphics, the process is: Selection box select Network → → → Stretching → drying → screen cleaning gel coating photosensitive printing → exposure → develop → Specific processes are as follows: 1. Net frame Usually aluminum, easy to operate, easy deformation strength. Stretching before wiping with cyclohexanone network box, and take off the residual oils and dirt, then wipe the alcohol industry, the last water wash, then dry and network box. Printed version in the network operation, the need to repeatedly dry and clean so the drying conditions should be strictly controlled. 2. Stretching At first, mesh, rubber, nylon mesh screen printing, ink over the net rate is good, constant tension, used to cover the net box device side and the more peripheral screen frame 6 ~ 10cM of the screen, using pneumatic Stretching Machine Stretching and six with the tonometer method for testing, to achieve the required tension, the coating adhesive to cement the screen frame screen, speed up the drying with hot wind, after about 5Minr cement, you can turn off the stretching machine, the excess wire glued to the outside network box, so as to help maintain the wire bonding fastness. Cut off excess wire with cyclohexanone, industrial alcohol, drying after washing face net. If the stretching tension instability may lead to Fonts deviation and fuzzy, there are strings substrate surface caused by differences in ink thickness. Xu Yong tension plane orthographic print large screen, there arc the printing surface tension of the small screen Xu Yong, process applications, screen tension range is 3N/cM ~ 7N/cM. General tension of the short life of a big screen, processes should be based on the need to use: printing conductive ink screen with a 100 objective straight yarn, printing orthography, blocks of color with the purpose of ramp 200 to 300 mesh, to ensure that the ink film thickness and Photo integrity. 3. Photoresist coating Commonly used hand-coating, the blank screen leaning on the wall, coated with stainless steel coating trough 2 to 3 times, angle of about 50 ° to observe the background layer with thickness measuring thickness. Scrape the black background on the orthography and the emulsion thickness of 20 ~ 25μM, a curved hollow print screen emulsion thickness of 28 ± 3μM, emulsion thickness of the different processes have different amount of material which should be taken, emulsion thickness must be uniform. Drying oven temperature at 40 ° or so, to avoid the high temperature will affect the performance a sense of optical rotation facilities, drying in the Process of security lighting, should use yellow lights, avoid white injection room, screen out exposure after drying 10Min . 4. Exposure Exposure is to non-graphic parts of the photosensitive film to light after a chemical reaction between the molecular structure of film cross-linked hardened. From the soluble into insoluble, develop resistance after the formation of optical layer (hard part) and transparent image of part of the mesh (no light sensitive glue is water soluble) to ink the printing surface through the formation of the mesh pattern. Exposure using the vacuum plate, a transparent tape affixed to the screen on film, emulsion side facing up, the template posted live footage, screen frame covered with black cloth, lay down their leather cover keeping the ventilation system (air pressure of about 110 120pA), such as air pressure stable, after the activation of skin exposure glass cover closely aligns device, according to the nature of light-sensitive plastic, film thickness, and the graphics crude Zan Yu-po delicate Ben Huan Mǔ? Industrial hygiene garden? 0S ~ 60S between. 5. Develop The screen will be exposed soaked with water 3 ~ 4Min, and then put some pressure on both sides of film rinse under water until ℃ ℃ ℃ clean the image part of the membrane to form the image completely transparent mesh up. Photo section Photo section with non-apparent, the hands touch the surface should be smooth and light feeling, not being dissolved traces of filtered water droplets sent drying oven. Screen proofing and general secondary to exposure to enhance screen life. 6. Redeployment ink Silicon rubber printing ink to be suitable for physical and chemical properties of silicone rubber, and printing can be firmly attached to the surface, which, like other ink from the pigments, binders, solvents by mixing, grinding wheel by the three liquid processed. Usually kerosene as a diluent, a single fluid ink curing agent added (trace amounts) to enhance adhesion and wear resistance of imprinting, two liquid ink direct printing. Save ink temperature control in the 0 ~ 10 ℃, high temperature drying after printing. 7. Printing Pre-press ready fixtures, screen, ink, clean and grease-free printing surface, the surface is too smooth to be by flame, corona treatment, to ensure good ink adhesion, good sun screen fixture fixed to the machine table printing of the keys on the jig fixation, blade hardness of the hardness of rubber should be quite (55 ° or so), regulation line position, the Web version proofing and regulatory rules on the line and the cover line aligned position to position accurately sample overlay. Adjust the distance between screen and printing surface, so scraping screen printed substrate can be a good touch, stroke of ink coverage must be greater than the pattern surface 2 ~ 5cM. Blade angle control between 75 ° and about printing to first article inspection, comparing samples, sampling time, to achieve full control of product quality. Third, technology of Screen Printing a copy of film location must correspond with the fixture, proofing and screen, the film in close contact with the screen to prevent the location of mobile, in the design process, the thin line the word should not get too close, otherwise easily lead to adhesion. Like to play background printing, general background smaller than the surface color 0.1 ~ 0.2M, so as to ensure that the printing surface fully covered, to ensure product quality. Screen Printing a copy of the above process, due to more flexible substrates, and the smaller screen of the tension, it is prone to fuzzy font, position closed, the thickness of different phenomena such as ink, in the process of dealing with these issues, must be carefully analyzed, with curved printing surface tension with a smaller screen, and the blade should not be too hard, the flow of ink is better (but to control the font thicker), Indian doctor blade of the scraper speed control in the 12 ~ 24cM / S. Printed products in the baking process, the need to control the furnace temperature and baking time well to improve the adhesion of the product. Silicone rubber screen printing is one of the more special, in addition to soft substrates to be equipped with a soft scraper, special ink work outside, in practice, the process needs to master the ideal product to print
|